Preserving environmental values has been at the heart of our mission since day one. Over the past decades, we’ve taken meaningful steps to promote sustainable development in the plastics industry and remain steadfastly dedicated to this cause.
We are determined to become carbon neutral by 2040, supported by a comprehensive long-term plan. As part of this initiative, we have acquired seven new electric cars, powered by our solar panels through an innovative Hungarian-developed charging system.
Carbon Neutrality by 2040
Energy consumption is the primary contributor to the carbon footprint of the injection molding industry, making its reduction a critical priority. This requires optimising energy use not only in production but also in offices and logistics.
As a responsible company, sustainable operations are fundamental to our values. However, we aim to go further for our environment: our goal is to achieve full carbon neutrality by 2040.
To achieve this target, we have developed a long-term programme focusing on eight key areas:
- Innovative product design
- Recycling
- Energy efficiency site improvements
- Reducing the carbon footprint of the plant
- Improving the energy efficiency of production
- Optimising travel
- Fuel-efficient logistics
- Fuel-efficient business travelling
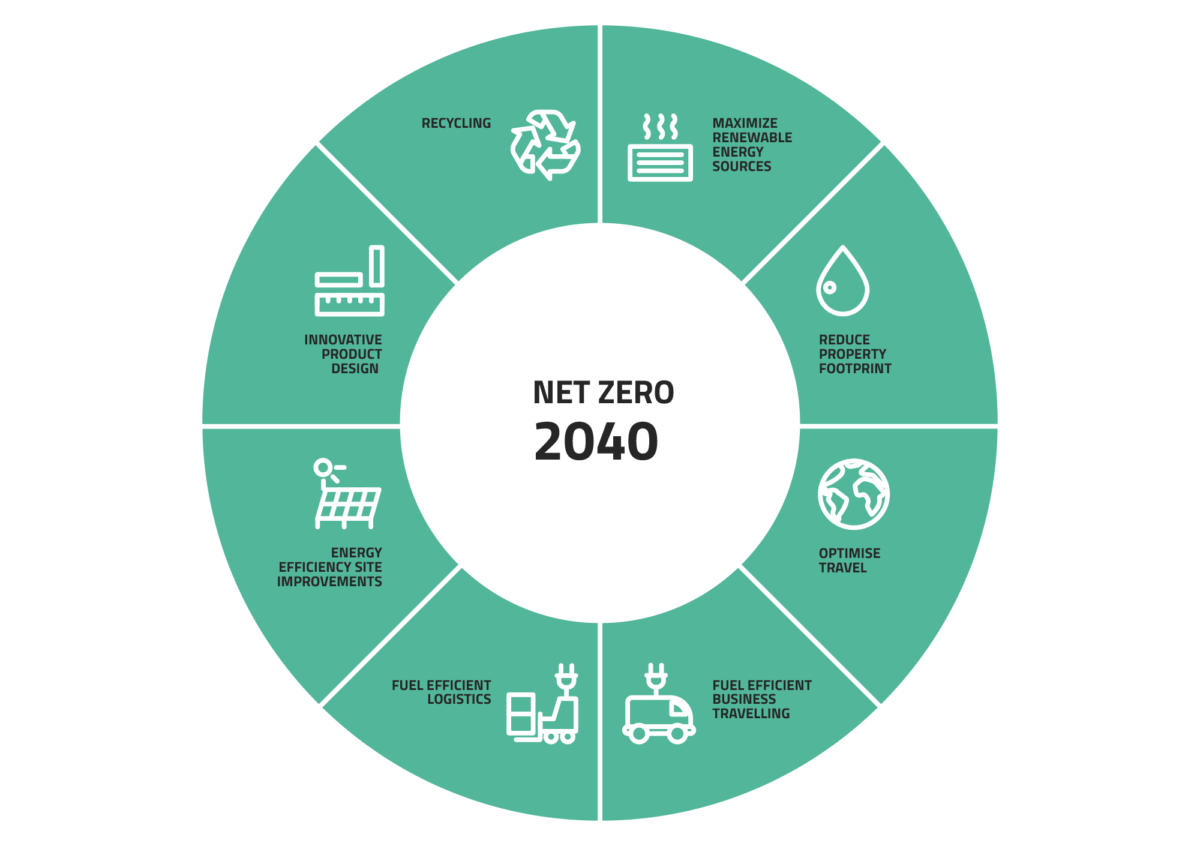
Our carbon neutrality goals set for 2040
Our latest investment: 7 new electric cars
We’ve made significant progress toward carbon neutrality across various areas. Beyond upgrading our production facilities, we’re continuously optimising energy use in logistics. As part of this effort, our fleet expanded in the fall of 2024 with seven electric vehicles:
- 5 BYD Seal,
- 2 BYD ATTO3, and
- 1 BYD Dolphin.
The new vehicles are powered by an innovative, Hungarian-designed “smiling” charger installed on-site, fuelled entirely by electricity produced by our solar panels.
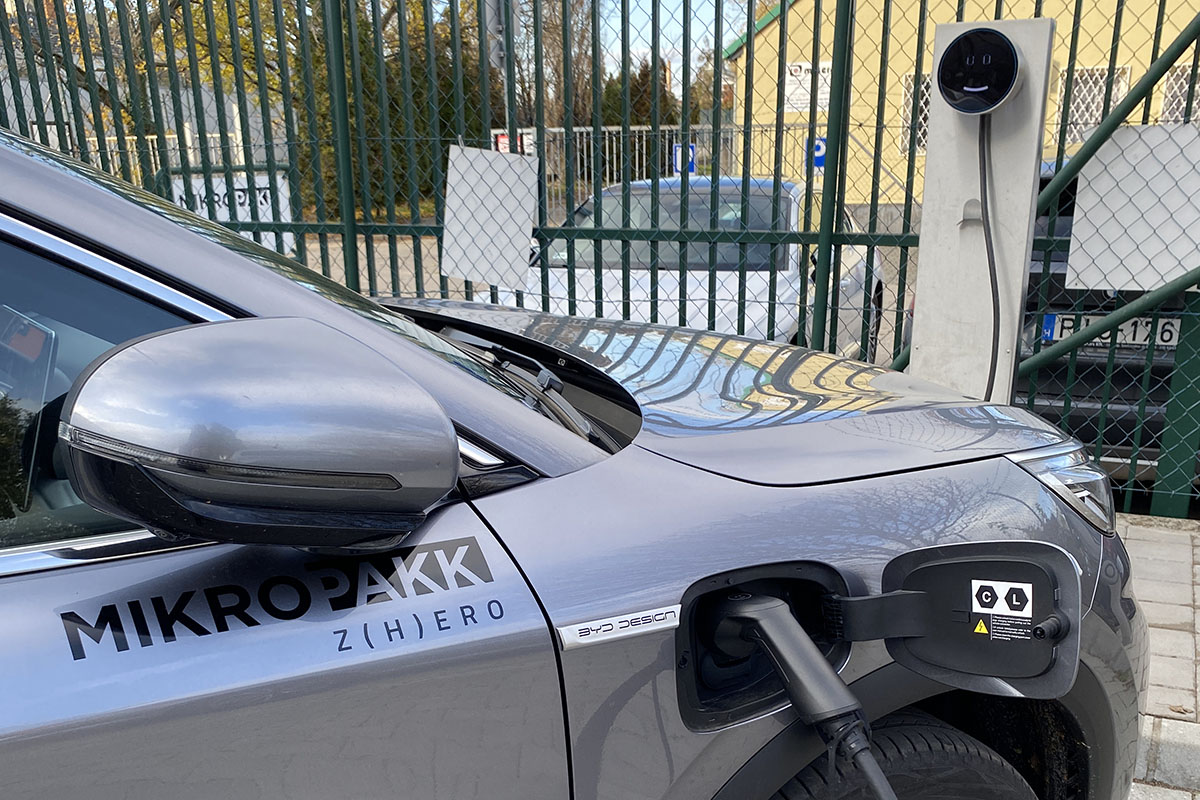
Both of our facilities are equipped with Hungarian-developed smiling chargers to power our cars
Our efforts for sustainable development
Even before announcing our carbon neutrality programme, we were deeply committed to improving the sustainability of the plastics industry and minimising its environmental impact. We are proud to have introduced a closed-loop water system for process water regeneration as early as 1997—meaning our facility has been entirely wastewater-free for over 25 years.
New, more energy-efficient injection molding machines
In 2005, we transitioned to fully electric injection molding machines, and by 2011, we had eliminated all fossil fuels from our production system. By upgrading our molding machines, we have reduced energy consumption per kilogramme of plastic product by 40%, significantly lowering our facility’s carbon footprint.
During the molding process, the heat carried away by the cooling water is repurposed to heat our offices, which no longer require any additional energy input.
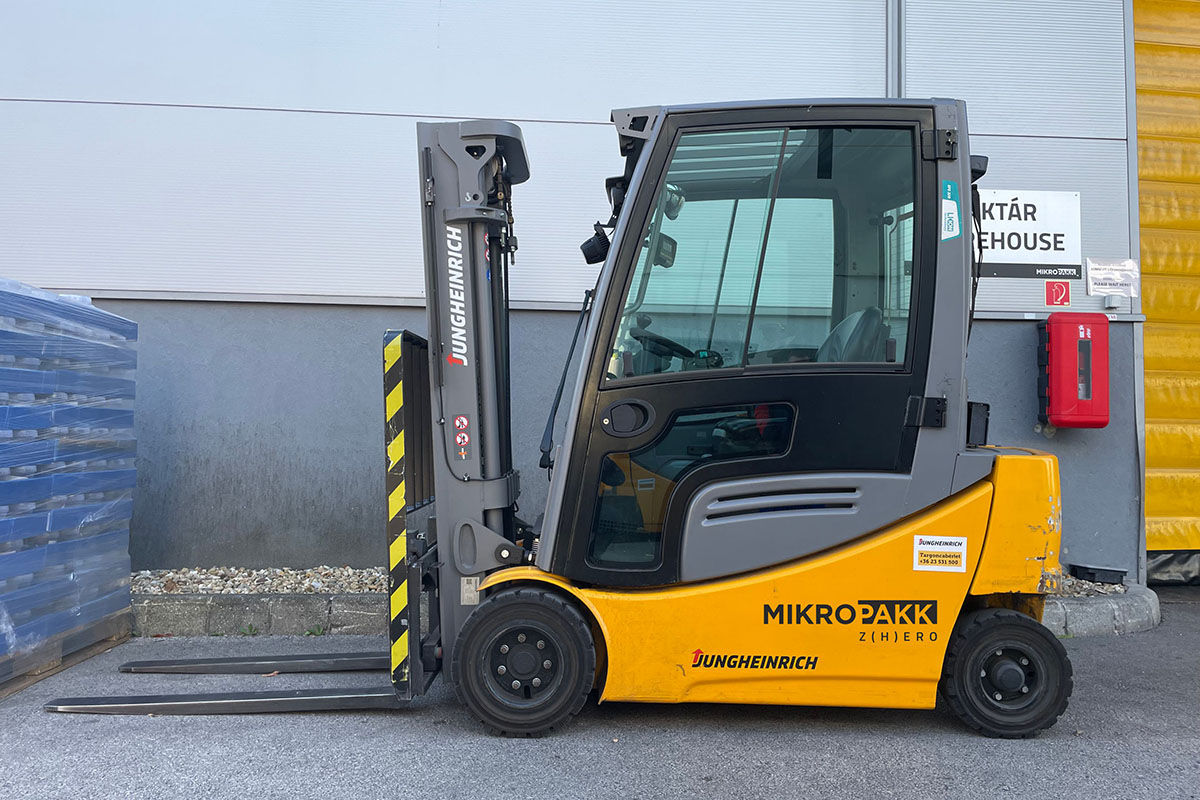
In 2021, we replaced our gas-powered forklifts with electric ones
Electric forklifts and solar panel system
In 2021, we replaced our gas-powered forklifts at our Budapest facility with modern electric models. These consume less energy, helping us further reduce our carbon emissions.
In 2022, we installed solar panel systems in both our Budapest and Salgótarján plants. The electricity generated is utilised efficiently—we don’t feed it back into the grid but use it entirely to power our internal operations.
Sustainable manufacturing at Mikropakk
We believe injection molding can be sustainable, and manufacturers have the greatest role to play in making it so. That’s why we prioritise minimising waste and creating opportunities for recycling during production.
Additionally, all plastic products can be made more eco-friendly by reducing their weight and the use of fossil-based plastics. With our two production facilities, we also optimise transportation routes, lowering the carbon footprint of delivering our finished products.