Non-professional users often rely on disposable PU foam dispensers for household tasks or hobby applications. However, with canister designs, applying the PU foam requires both hands, which can be cumbersome. To address this issue, we developed the Genius integrated hand adaptor. This product is manufactured in our Mikropakk BLACK facility in Salgótarján, and is produced by the millions annually, entirely automated, in-line.
In the following, we will introduce:
Objectives and capabilities of the Genius Integrated Hand adaptor
The aim of the PU foam dispenser adaptor development was to create a product that allowed for easy one-handed use and offered at least 6 weeks of reusability. The resulting spray head features a “Stop & Go” function, meaning that after use, the integrated hand adaptor can be resealed to prevent accidental dispensing. Furthermore, the dispensing tube can be folded and sealed, allowing for multiple uses of the canister.
During the design of the product closure, a primary requirement was to facilitate the safe dispensing and application of PU foam in all aspects. To this end, the spray head holds two packaged protective gloves within and includes a plug that can be broken off, allowing the dispensing tube to be sealed airtight after use. Thanks to our product development, we now manufacture this highly successful and popular product with a complementary part, that ensures finer dispensing.
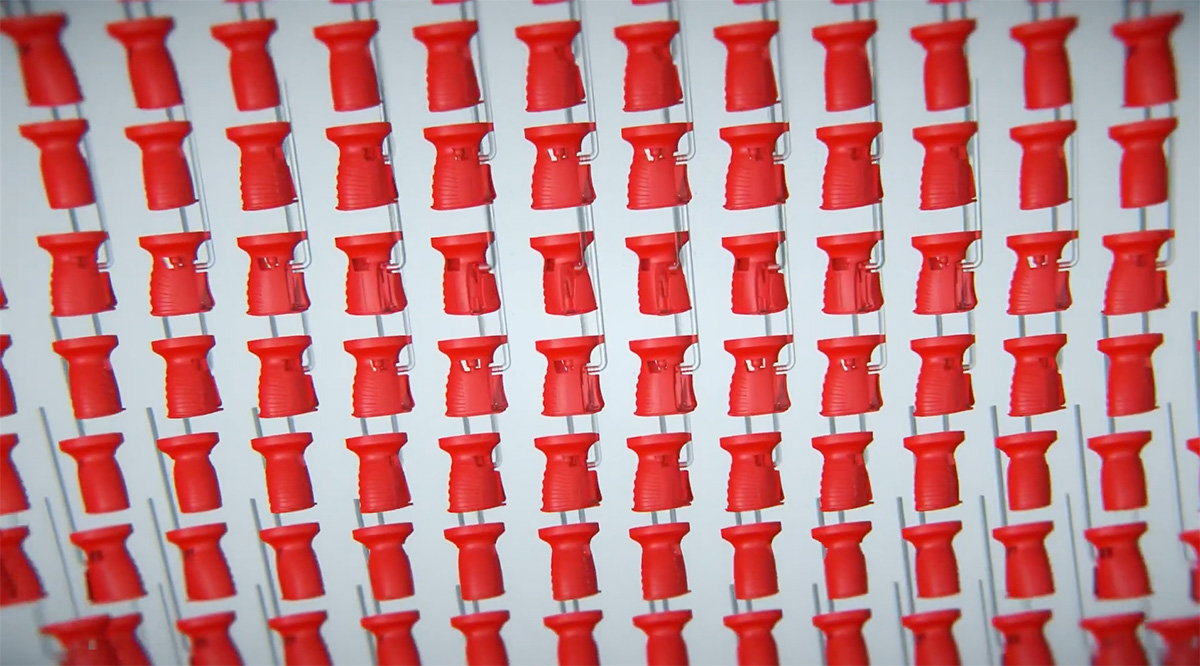
Automated production of the multi-component, injection moulded spray head
We fully automated the production of the integrated hand adaptor, enabling us to manufacture it by the millions, annually. Production runs continuously on 3 injection moulding machines, 365 days a year, only winding down for scheduled maintenance. Following the moulding process, a robot transfers the spray heads to the automated assembly station, where the glove is inserted, and the transparent dispensing tube is attached to the adaptor. This tube is then automatically folded by the machine for easier packaging. To ensure impeccable quality, the process continues with automated leakage and blow-through tests.
After the tests are completed, the robot places the finished product into the box. Once the box is full, an operator is responsible to swap it with an empty one. Additionally, the operators’ tasks include tray-loading the packaged gloves, positioning them for pick-up and refilling the tube dispenser.
Development of our injection-moulded products doesn’t end with the start of mass production
We continuously monitor feedback, ensuring that development remains ongoing. Thanks to this approach, we found a solution when packaged gloves occasionally fell out of the adaptor during transport or packing. By increasing the size of the gloves, this issue was resolved. Another problem encountered was some of the folded dispensing tubes popping out of the retaining tab. This required a redesign of the hand adaptors’ structure, necessitating modifications to both the injection moulding tool and the assembly robots’ design.
In addition to these challenges, we have enhanced the efficiency of automated production, allowing us to operate with shorter cycle times and even greater precision. These achievements motivate us to continue our developmental efforts in the future. For example, an exciting area awaiting exploration is the use of regranulates.
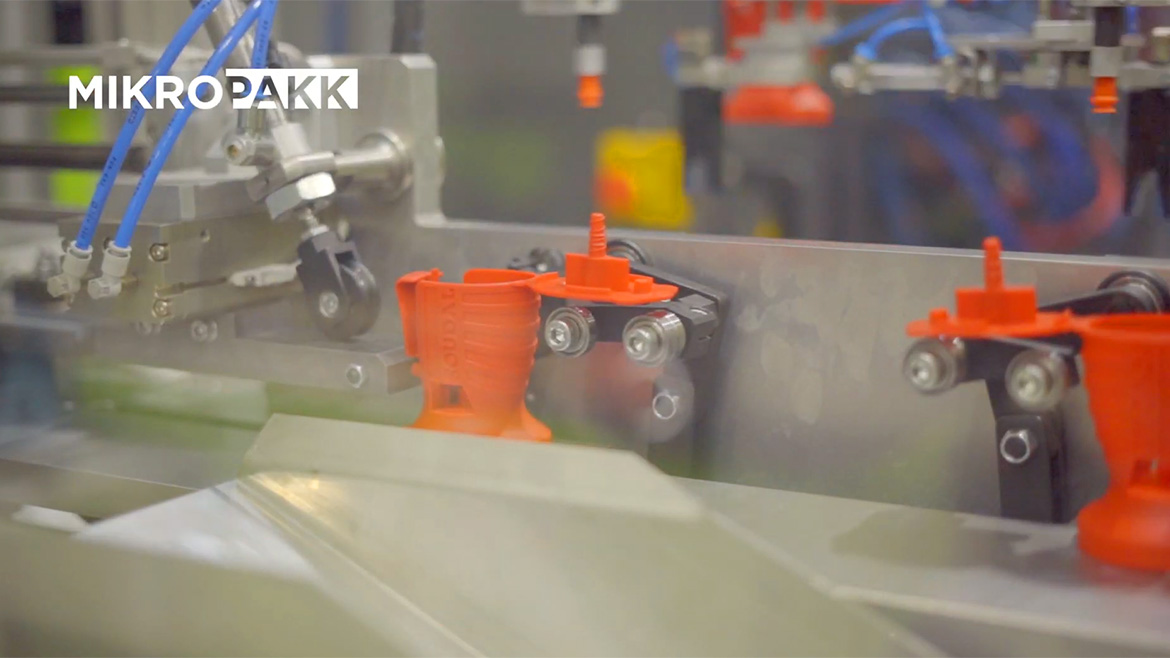
Development and manufacturing of high-quality plastic components
At Mikropakk, we believe it’s essential that development doesn’t cease with the start of the product manufacturing process. Our goal is to deliver innovative products using the cleanest, most efficient production methods possible. That’s why we place significant emphasis on factory automation, which helps achieve the desired high quality, both in the production process and in the standard of the finished products.