Mikropakk is manufacturing, assembling, and pad printing the decoration of the plastic applicator for a medical device for the pharmaceutical company Richter Gedeon. The device, that provides automatic medication dosage, was designed with the consumer in mind. Therefore, in addition to smooth handling, a pleasant touch and aesthetic appeal were essential aspects.
For the production and assembly of the plastic applicator, we have built a new semi-automated production line at our Budapest site, Mikropakk SILVER. In the future, we plan to upgrade the current production line to a fully automated assembly process, replacing human workforce with a robotic cell.
In this case study, we describe the different levels of automation and how it is done on a semi-automated production line, through the manufacturing process of this plastic applicator:
The Lenzetto spray medical device
Lenzetto menopause hormone spray provides a convenient and accurate dosage for hormone treatment. A dispensing spray in the applicator ensures proper delivery of the product, that is absorbed through the skin. The applicator is push-button operated, making it easy for the user to measure out three button presses per dose, and after use, the lid closure ensures hygienic storage.
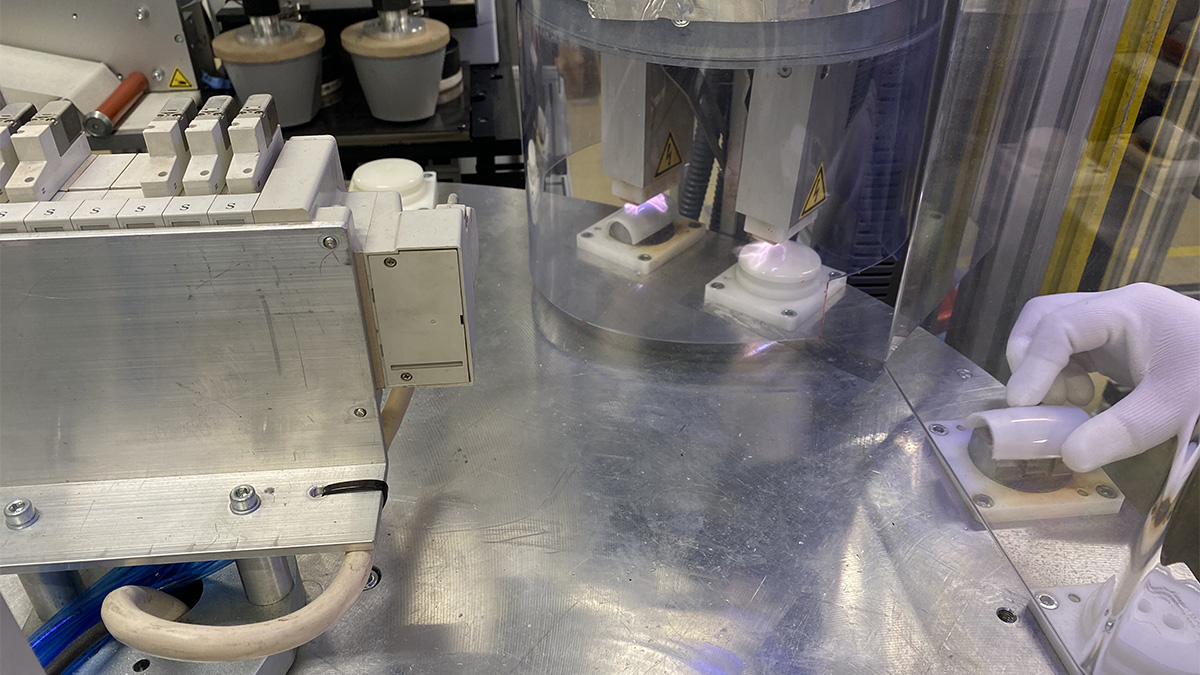
Semi-automatic assembly of injection molded parts
Assembly of nozzle and injection molded parts on a semi-automated production line
Lenzetto applicator parts are injection molded and further optimised on a semi-automatic production line based on operator feedback. After ramping up production, with full automation, it is possible to meet especially high demand, even up to a target of five million parts per year.
A key aspect in the design of manufacturing and assembly processes is the integration of quality control, that is applied at multiple points in the production process. Ensuring that the applicator is assembled using quality-controlled components in all cases. In order to avoid additional error possibilities, tasks that require high precision are performed by a fully automated production line.
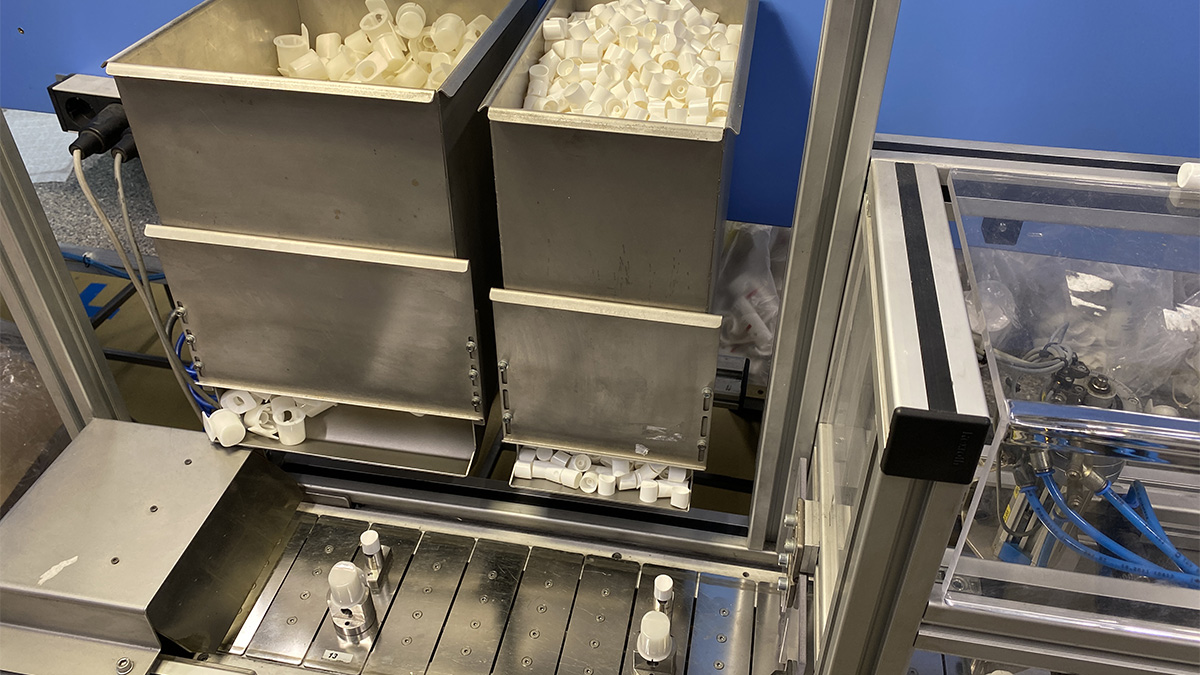
Elements of the applicator nozzle before assembly
Automated spray nozzle assembly and quality control
The applicator nozzle is assembled on an automatic assembly line. An operator places the parts on the machine’s conveyor belt, which are then turned in the specified direction by the machine and checked through a camera gate. After the inspection process, the machine assembles the two parts and quality control is carried out again. This allows defective caps to be immediately detected at the end of the process.
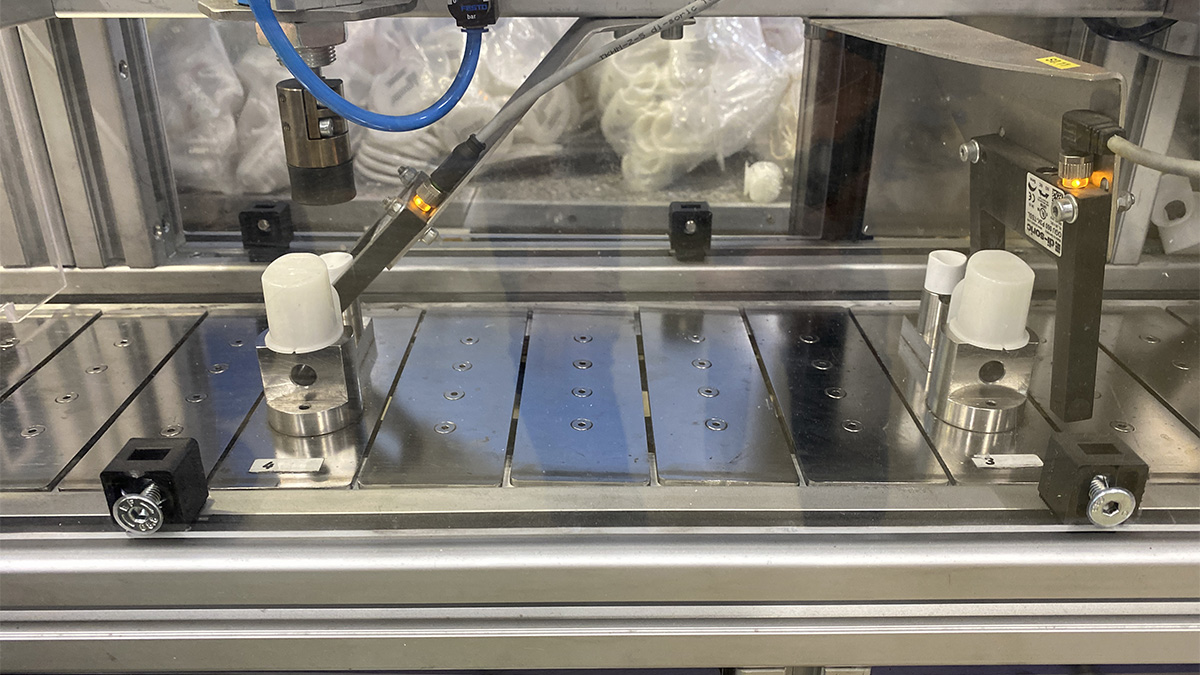
Quality control of parts via camera gate
How injection molded parts are assembled
The plastic parts are placed on the clamps of the turning table by an operator. The parts are then surface-treated with plasma to obtain permanent paint adhesion.
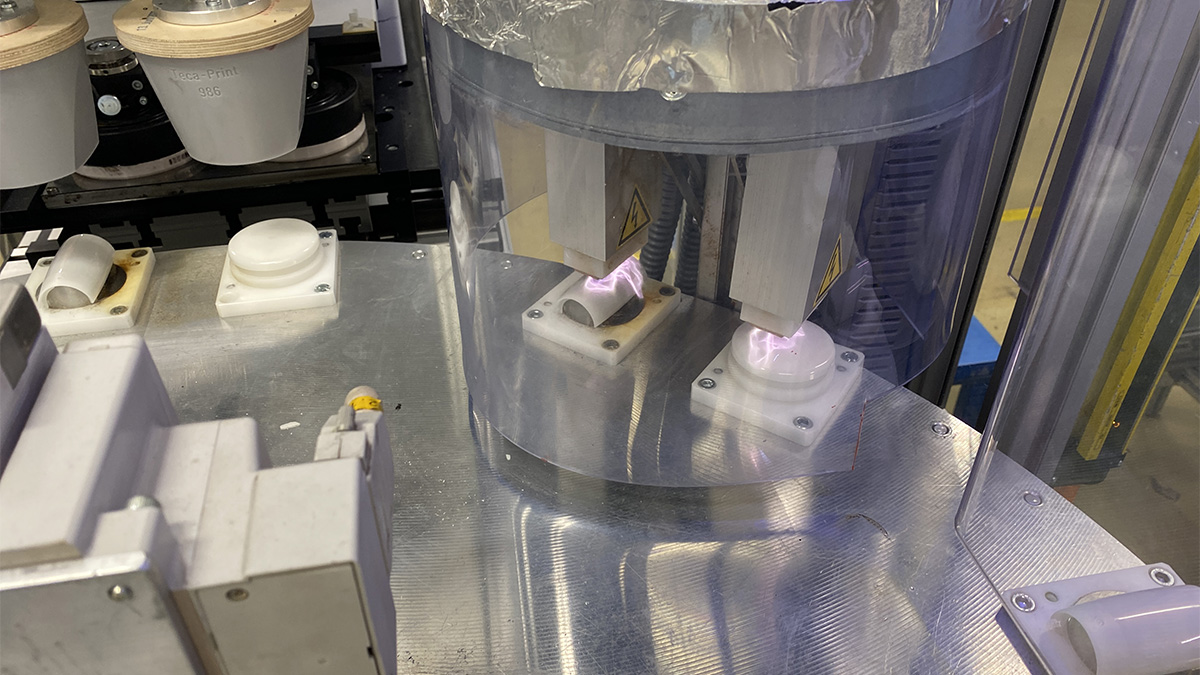
Degrading the surface of the plastic part with plasma for better adhesion
Integrated into the assembly process, pad printing allows 37 different languages to be printed on the surface of the plastic parts. The curing of the golden-yellow brand name can be accelerated by using an infrared lamp.
A film coating is applied to protect the surface of the applicator. Followed by ultrasonic welding of the packaging crucible, an operator checks the quality of the finished product and applies the sealing cap.
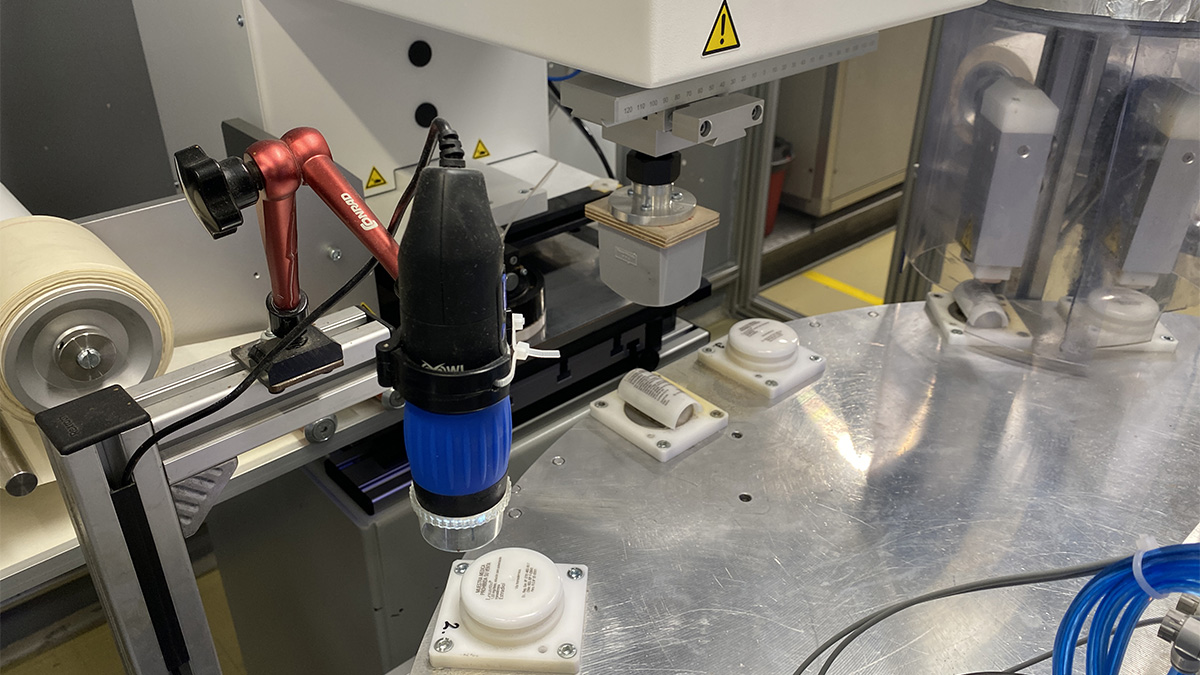
Decorating injection molded parts by pad printing
Precision assembly of injection molded plastic parts even for medical applications from MIKROPAKK
We offer customised industrial automation, as well as assembly and decoration after the parts have been manufactured. For our services, we build customised production lines at our own sites to achieve maximum efficiency.
We offer high-quality, custom-designed nozzles and injection molded parts assembled from a wide range of components.