At Mikropakk, plastic product development has been at the core of what we do for over 20 years. In a market where speed, cost-efficiency, sustainability, and reliability are expected, we help our partners bring plastic products to life – from concept to mass production.
We continuously explore smarter packaging and product solutions, often saving clients 20–50% through better design and process optimization while enhancing packaging benefits for end users.
How we approach plastic product development
Our work is grounded in over 30 years of hands-on experience in mold design and injection molding. We focus on practical, cost-efficient solutions tailored to each project.
We’ve been running our in-house R&D&I team since 2006 and our automation department since 2009. Today, we operate with a focused and experienced team of engineers and involve trusted external partners when specialized expertise is required.
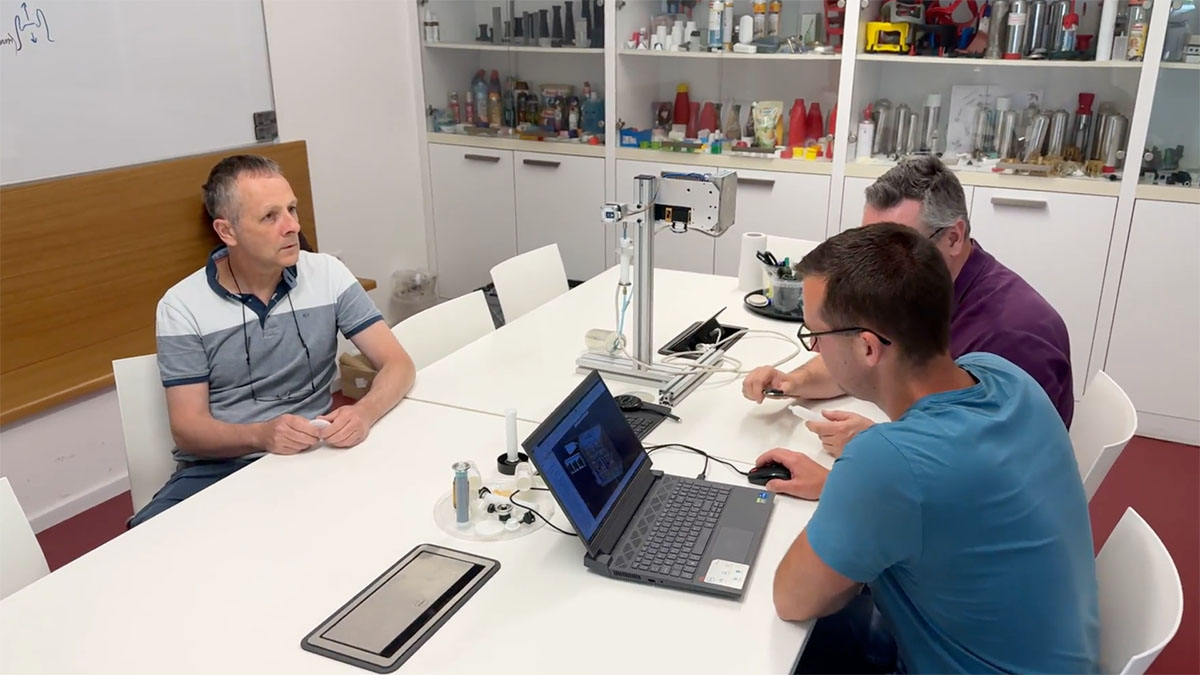
Our R&D team works closely together – from design to automation
Duo core strategy: manufacturing meets innovation
Plastic product development at Mikropakk follows a dual-core strategy:
- scalable, high-volume injection molding and
- parallel product and process development to improve cost and efficiency.
That’s why we’ve added automation to our production. Being a mid-sized company, we make quick, flexible decisions. Our CEO also leads the R&D team and evaluates each project carefully.
If a project shows strong technical and commercial potential—whether it’s a client collaboration or an internal idea—we’re ready to invest. This might mean allocating engineering time, adjusting our production setup, or acquiring new equipment. We have the resources and stability to act when we see long-term value.
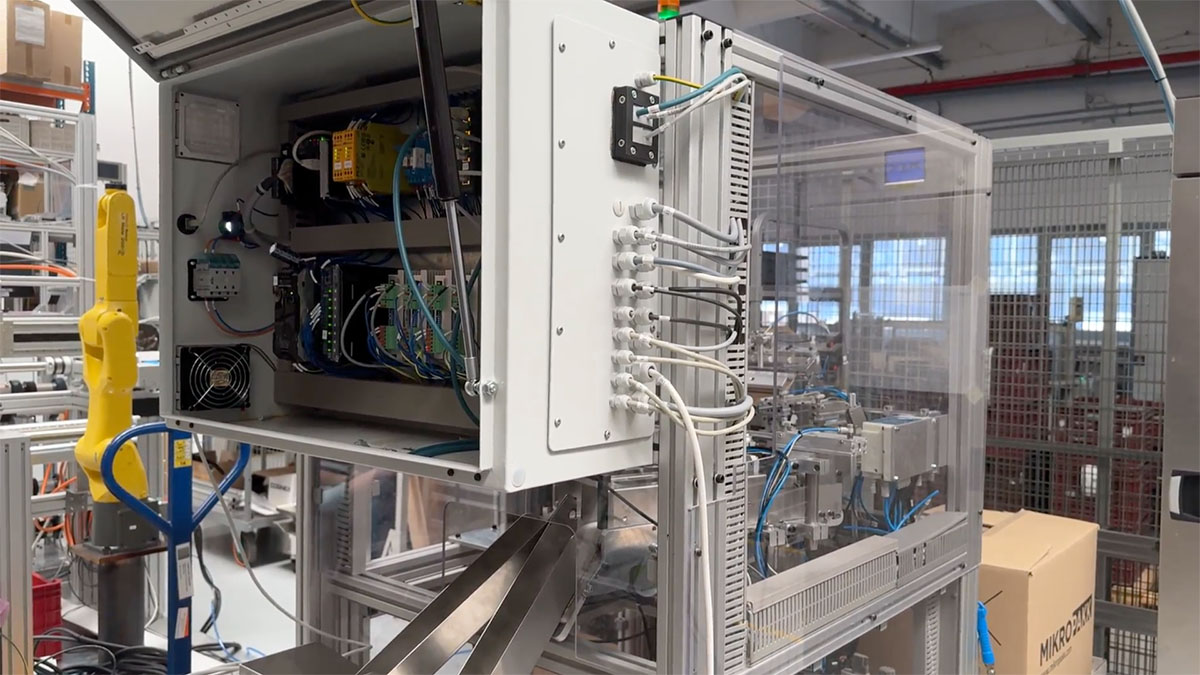
From concept to production – we turn good ideas into working machines
We proactively suggest improvements; we bring ideas to the table that improve efficiency, sustainability, and cost, end-user benefits.
Around 4% of our revenue goes into R&D&I, because we believe the greatest long-term value lies in developing competitively priced, highly functional, and manufacturable products.
Plastic product development from idea to production
Our product development process is structured yet flexible. It may start with a client, a partner, or an in-house idea. The first step is always a brainstorming session, followed by concept design with the help of our industrial designer, an expert who understands injection molding, ensuring manufacturability is part of the design.
Once a concept is approved, we turn it into a SAFE model, then 3D print a prototype, and create a pilot mold to produce a few thousand test units. If everything works, we scale up to full production.
Throughout the process, we use simulation software, material tests, and in-house testing. We also have a small internal lab equipped with a furnace and testing cabin. For more complex projects, we rely on collaboration – knowing when to bring in external expertise is part of our competency.
We focus on product optimization – sealing edges, ribbing, and material thickness – to ensure the final product is both functional and economical.
Since we manufacture plastic components for a range of applications, we’ve run parallel tests in key areas using PCR materials to gather insights. This hands-on experience has given us a clear understanding of where PCR makes sense — and where it doesn’t.
For example, in the food industry, food-grade PCR isn’t currently available on the market, so it’s not yet a viable option. Still, our experience allows us to support both current and future customers in their new product development efforts.
Designing for sustainability and scalability
Each plastic product development project starts with bottleneck analysis. If needed, we design semi- or fully automated assembly lines to ensure the process scales smoothly.
We also explore multi-material solutions, combining plastic, paper, and metal in one product. These are designed for easy disassembly and recycling at the end of the product’s life.
In the Henkel RE-NEW 2.0 project, for example, we created a structure that separates aluminum from plastic packaging, making both parts recyclable.
Learning through development
Not every product we develop reaches the market, but every project teaches us something.
We once redesigned our GENIUS GUN PUR foam dispenser using PCR plastics. The recycled parts differed in color from the original red ones, which the client wanted to keep. That led to challenges with color consistency and eventually to a solution that balanced sustainability with branding.
Have an Idea? Let’s Build it Together
Whether you’re launching a new product or want to automate a production process, Mikropakk is ready to help, from concept to manufacturing. Our team gets involved early to make sure the solution works well.
Contact us if you’re looking for a partner who doesn’t just build your idea, but helps make it even better.