The complexity of our services is well illustrated by one of our latest projects, the Henkel RE-NEW 2.0. It started with pre-production product development in close cooperation with our customer.
RE-NEW 2.0 is aqueous-based, single-component silicone in a specially designed 80 ml plastic tube for the renovation of silicone joints in households. Due to the tubular design, the silicone that cures at room temperature is easy to apply and correct on both horizontal and vertical surfaces. RE-NEW
- covers discolouration,
- fills in minor blemishes and
- provides excellent resistance to mould.
With innovative packaging, designed by our R&D team, RE-NEW makes it easy to renovate silicone gaskets at home.
In addition to injection moulding of plastic products, we also contribute to our customers’ development projects with our experience in product, packaging and process development. It enables us to support our customers in the production process with product design, tool design and even the design of automated production and assembly cells.
In this case study, we give an overview of this extra added value through a successful project, and show what:
Henkel’s packaging challenge
Henkel Adhesive Technologies manufactures adhesives, sealants and functional coatings for both industrial and consumer applications. Innovation plays a key role in their product development, therefore the adhesive and sealant range has been redesigned and renamed to “Henkel RE”.
The new RE range has been designed with the aim to create an environmentally friendly and precise solution. Henkel is committed to actively promoting the circular economy, thus RE products are designed to be recyclable, in packaging and in ingredients as well.
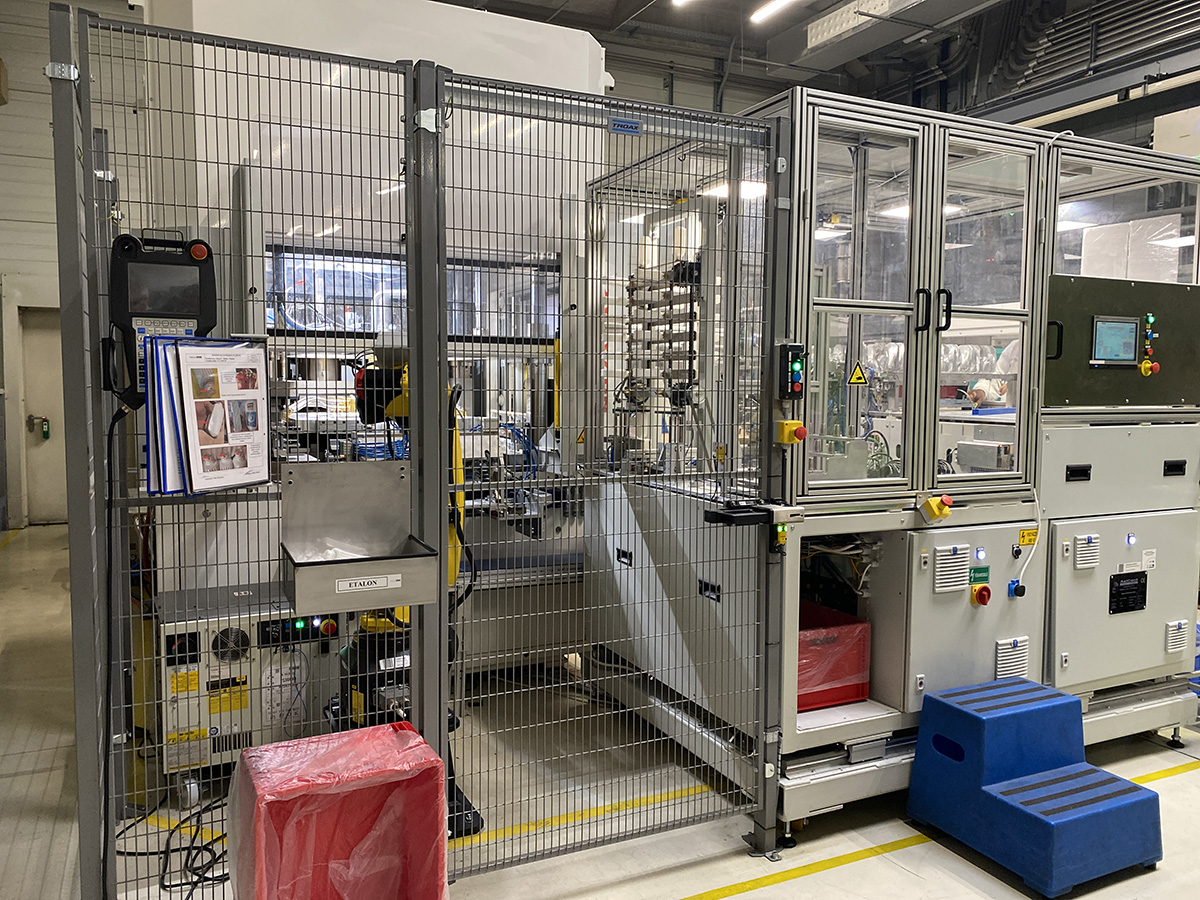
Fully-automated assembly cell
The role of the Mikropakk R&D team
Mikropakk’s plastic packaging R&D&I product development engineering team also assisted Henkel in the development of the RE-NEW product, as well as in the design of the product components, automation of the assembly process and quality control design.
In addition to sustainability, other criteria for the product was the design of a special, ergonomic application tube that:
- does not absorbs silicone,
- allows even dispensing and
- precise application.
Mikropakk’s solution: innovative RE-NEW packaging
The Bag On Valve barrier packaging technology allows easy use of the joint repair silicone and offers a clean end result:
- does not make the surroundings sticky or messy,
- easy to use several times without the residue sticking,
- does not require extra equipment or additional help.
The components of the innovative 5-piece packaging solution are the ergonomic, accordion-sided bottle, that ensures even and continuous bubble-free dispensing, the multilayer laminate bag, the 2K dispensing and smoothing cap, that is designed to allow uniform distribution and spreading on the surface, and the closure.
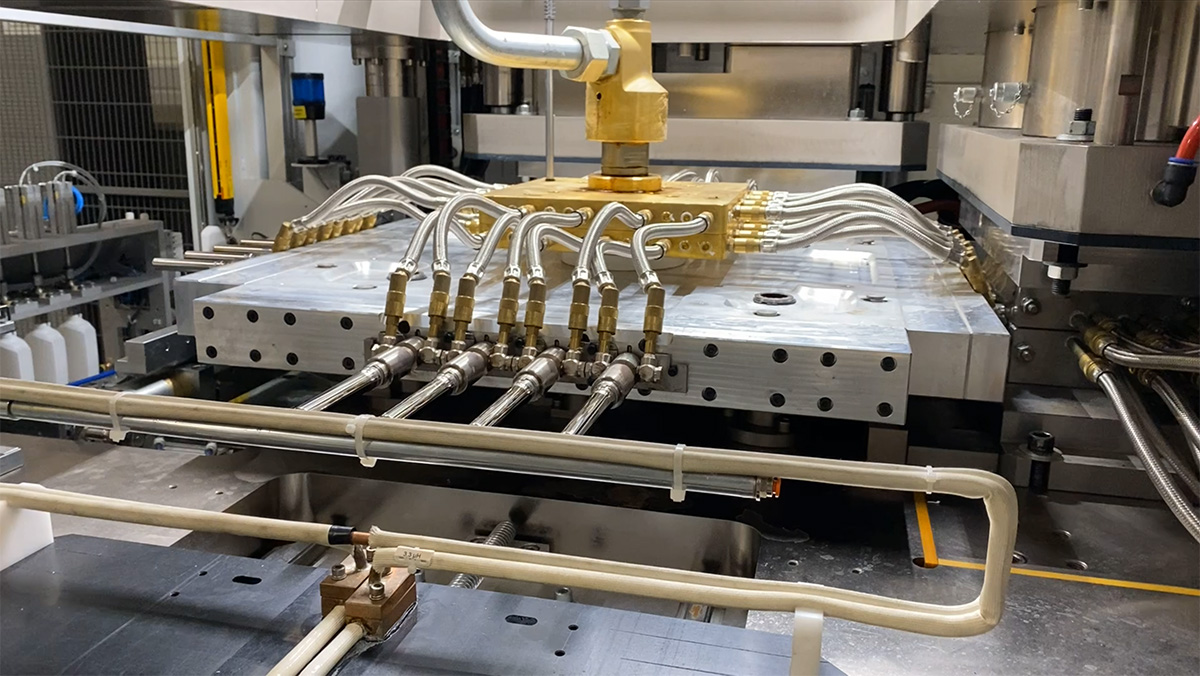
4 cavity injection blow moulding machine
Overview of the Henkel RE-NEW production process
Injection moulding and blow moulding machines are integrated into production and assembly cells, thus the plastic product is automatically assembled immediately after production in the manufacturing plant.
The bottle product can only be manufactured with IBM (Injection Blow Moulding) technology in the proper quality, therefore a new 4-cavity injection moulding machine was purchased for production.
The new machine is equipped with industry 4.0-compliant monitoring inputs and outputs, and is able to securely connect integrated robot and assembly cell.
The production process of components
The RE-NEW product consists of five components, four of which we are able to produce with our current capacity, and one of which is supplied by our partner company.
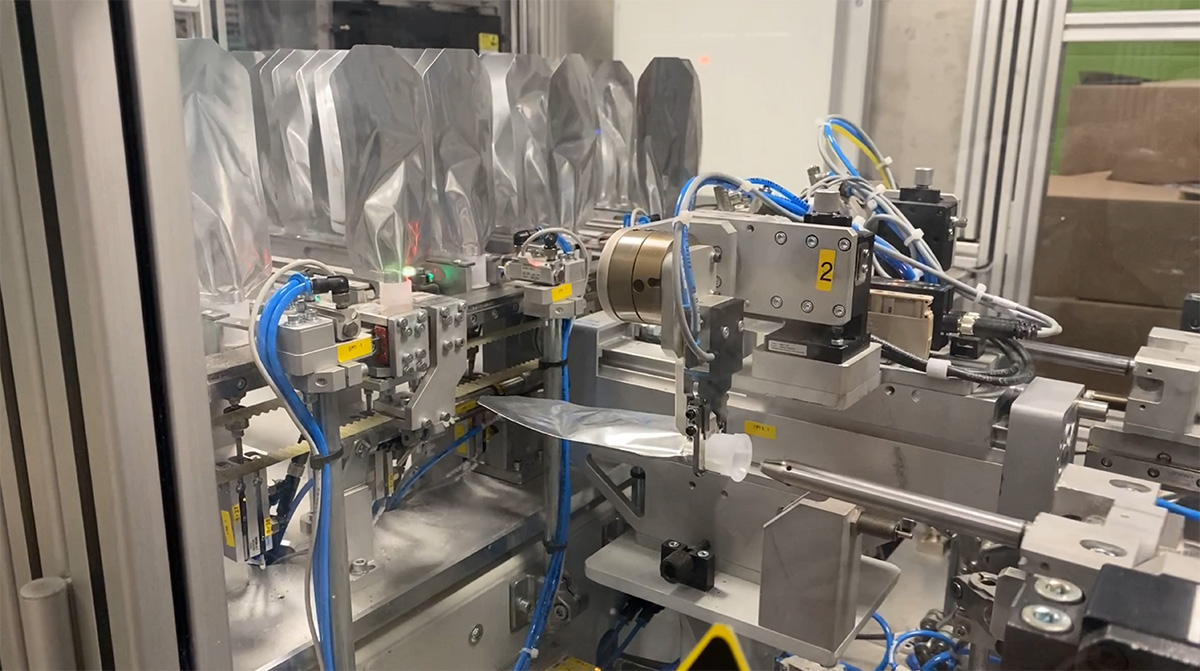
Multilayer foil bag
The packaging bag used in the product consists of a multi-layered film that facilitates the dispensing of the material from the bottle. Furthermore, it provides both oxygen and moisture sealing, thus ensuring the shelf life of the filling. The fitting adapter to the tube, i.e. the holder insert, is welded together using a custom-built target machine capable of dispensing, fitting and welding the two components together.
The final product requires a second automated assembly step when the machine inserts the welded bag into the tube.
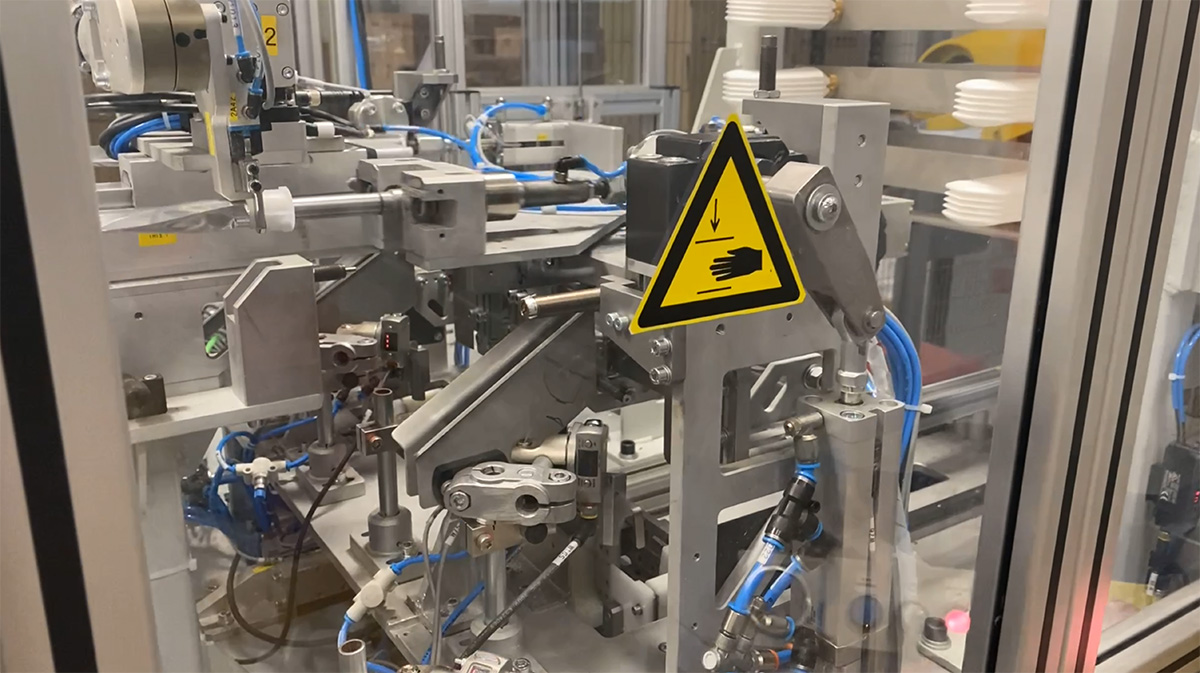
Inserting the pouch bag into the bottle
2K cap for user convenience
The RE-NEW has a specially designed smoothing spout to enhance the application of the product. Its manufacturing process is carried out by a 2k injection machine, the first of which is the injection moulding of the applicator body then a smoothing tip made of TPE is applied to the cap to ensure easy dispensing and a smooth finish.
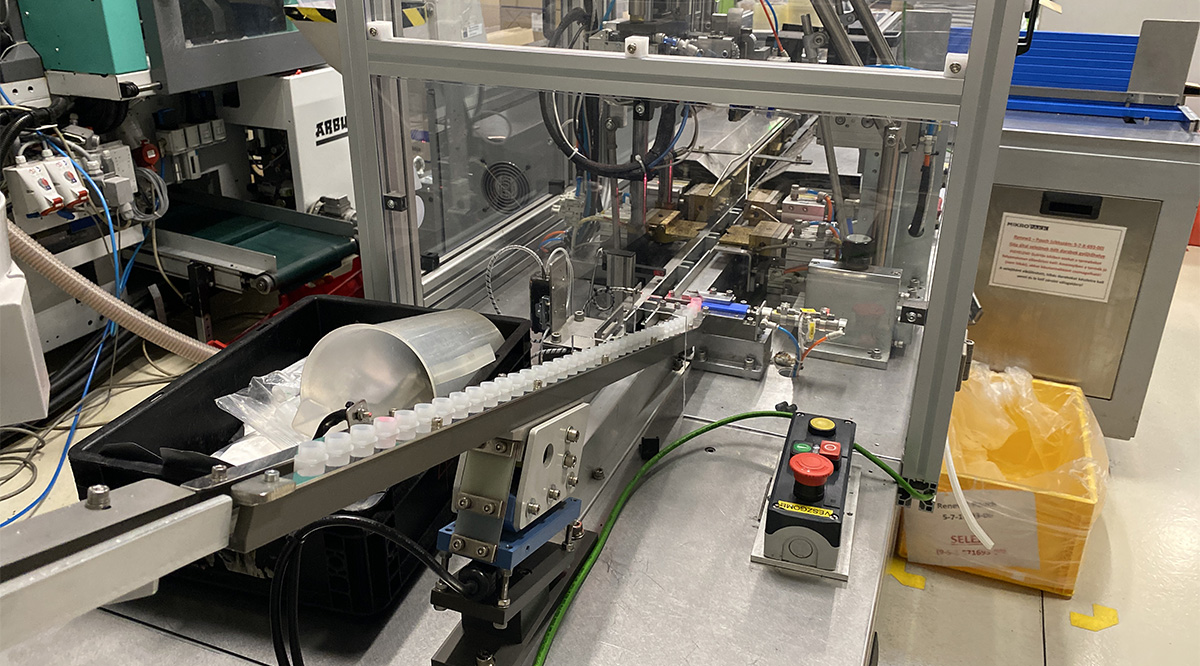
2K injection moulded cap
The machinery needed for mass production
Due to the complexity of the task, the quantity required by the customer could only be achieved with a highly automated assembly cell. To implement mass production, target machines were needed to perform various tasks.
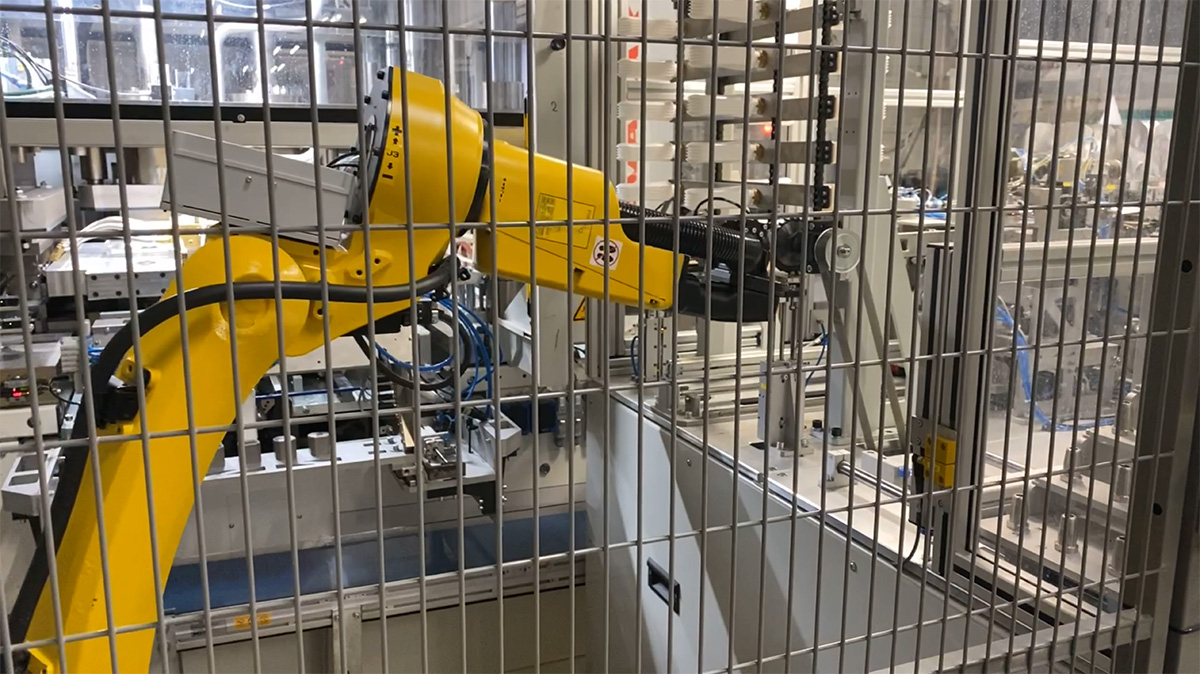
Robotic cells integrated into the production process
- Injection blow moulding machine for the Bottle parts
- Integrated robot cell – takes the pieces produced by the injection moulding machine.
- Cooling template – preserves the geometry of the product before assembly.
- Automatic welding machine – welds the multilayer pouch to the injection moulded smoothing spout.
- Automatic folding machine – inserts the bag folded in a specified way into the tube.
- 2K injection moulding machine – produces the dispensing cap in 4 cavities using 2 different materials with different properties.
We use the welding machine to produce only the number of bags needed for assembly, thus minimising the stock of parts to be installed.
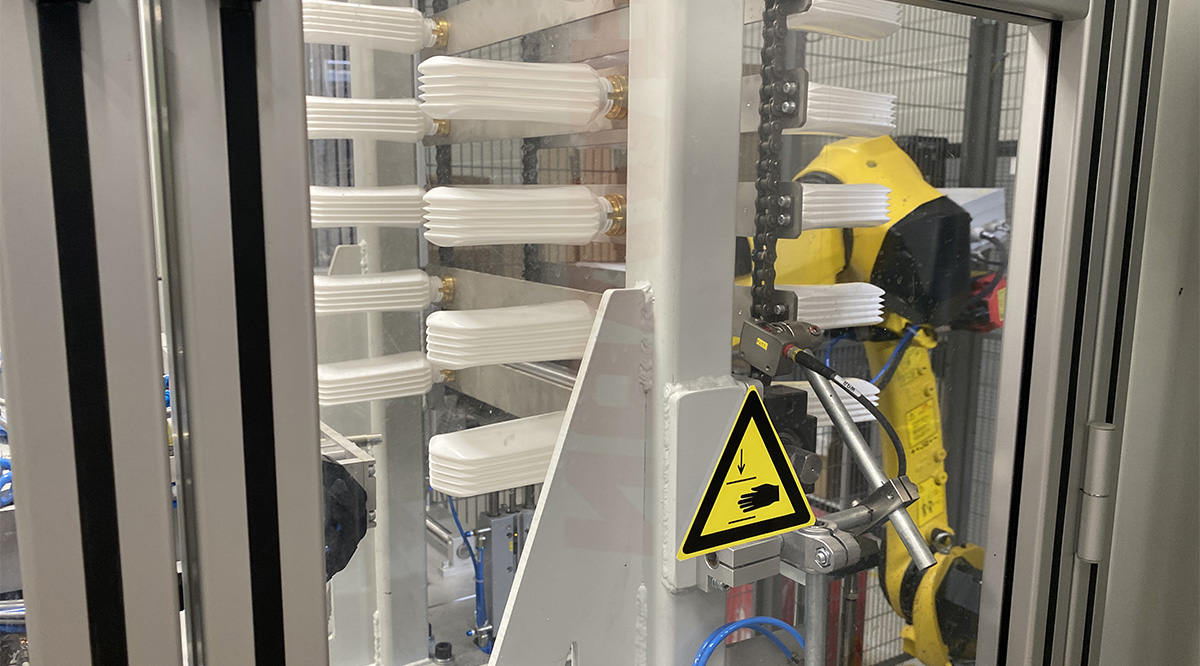
Cooling template to preserve the geometry of the products
Our quality control solution
After assembly, the last essential part of production is quality control. A common problem is that the inspection and packaging of products manufactured with short cycle times takes time and are carried out by operators, resulting in a lack of concentration of workers due to the constant monotonous work.
To avoid that risk, quality control and packaging workflows are carried out using a universal robotic cell. It is able to pick up the moulded products on the assembly line and, by means of a multi-axis movement, show the qualitatively important parts of the product to a camera.
The machine vision camera:
- measures the functional dimensions of the product,
- checks for colour defects, and
- detects missing pieces.
The product specificity of the robotic cell is the interchangeable arm, which can be exchanged to enable the robot to handle other products. It can be used to increase the output of products with short cycle times, while automatic packaging improves productivity stabilisation.
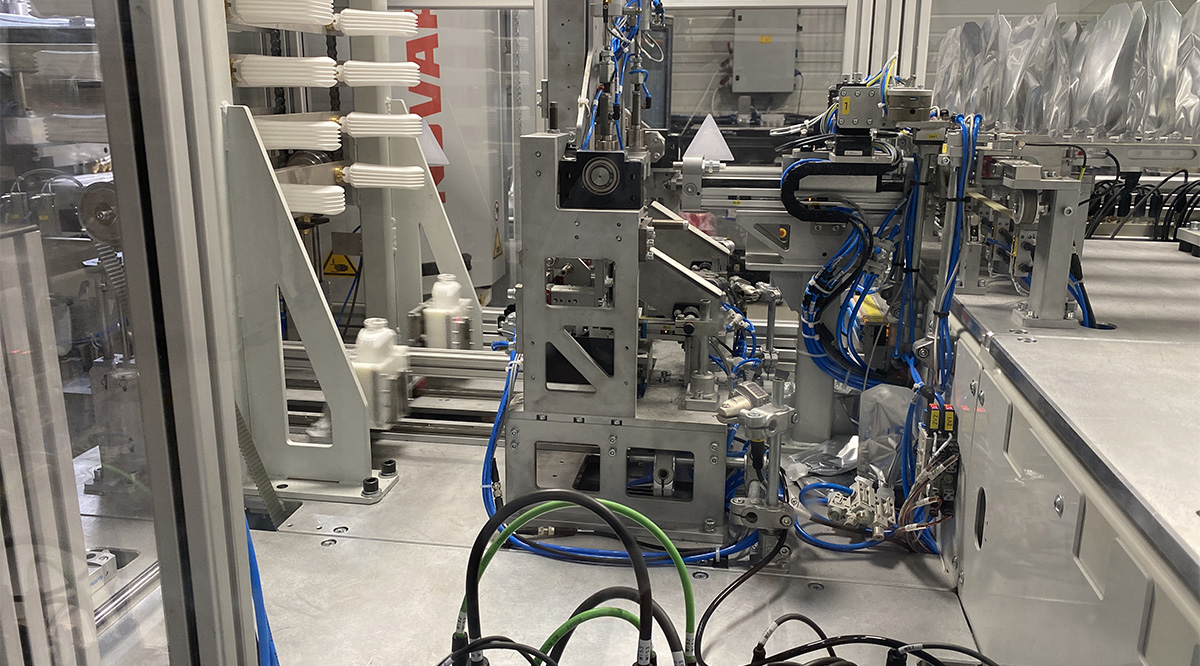
Target machines for mass production
Innovations at Mikropakk
We are proud to have a 30-year history of excellence in engineering and R&D&I, delivering innovative packaging solutions that give our partners a competitive advantage and support them with unique packaging solutions.