Quality service and product excellence are vital for achieving market success. They distinguish your company from competitors and foster long-term brand loyalty.
Developing quality assurance communicates a clear commitment to excellence. This commitment not only enhances your market position but also boosts internal workforce, maintaining a professional and motivated environment. At Mikropakk, we believe excellence in quality assurance is the key when it comes to plastic component manufacturing regardless of the field of use of the end product.
Ensuring high product quality with multi-level quality control
At Mikropakk, our commitment to quality is fundamental to our operations and strategy. Our certifications demonstrate our commitment to excellent quality products and services.
- ISO 9001 quality management system
- ISO 14001 environmental management system
- BRC-GS Issue 6 global food industry standard
Our certifications guide our team and affirm that our services meet stringent external requirements. By adhering to Total Quality Management (TQM) principles, we consistently meet our customers’ expectations, that is crucial for our sustained success.
Total Quality Management – The meaning of TQM
Total Quality Management (TQM) aims to exceed consumer expectations and enhance organisational performance continually. It involves every team member in managing processes effectively and fulfilling needs comprehensively. This strategy boosts consumer loyalty, streamlines problem resolution, and promotes a positive work environment.
Our quality control processes
We tailor the quality control processes for our products to meet the unique needs and specifications of our partners throughout manufacturing. We implement these processes at three distinct levels to consistently ensure top-quality assurance.
The first level of quality control uses online sensors and cameras on the production lines to monitor each product against specified parameters. Products failing to meet these standards are automatically removed by the system.
At the second level, our operators perform visual inspections based on a predefined sampling plan for each product at set intervals, recording the results in a real-time electronic system.
The third level involves more detailed examinations conducted by quality inspectors, including:
- microscopic visual inspection,
- manual measurement of dimensions using measuring tools,
- various functional tests.
In addition, at the client’s request, we implement Statistical Process Control (SPC) and compile various documentation, such as PPAP files. We issue a quality certificate for each product, defined by the client’s requirements.
Each production batch is assigned a unique identifier to facilitate easy traceability. We also store specific product samples at the beginning and end of production (start and stop samples) to aid in tracing should any issues arise. During every production run, we conduct machine startup checks as part of our line clearance procedure to prevent manufacturing defects.
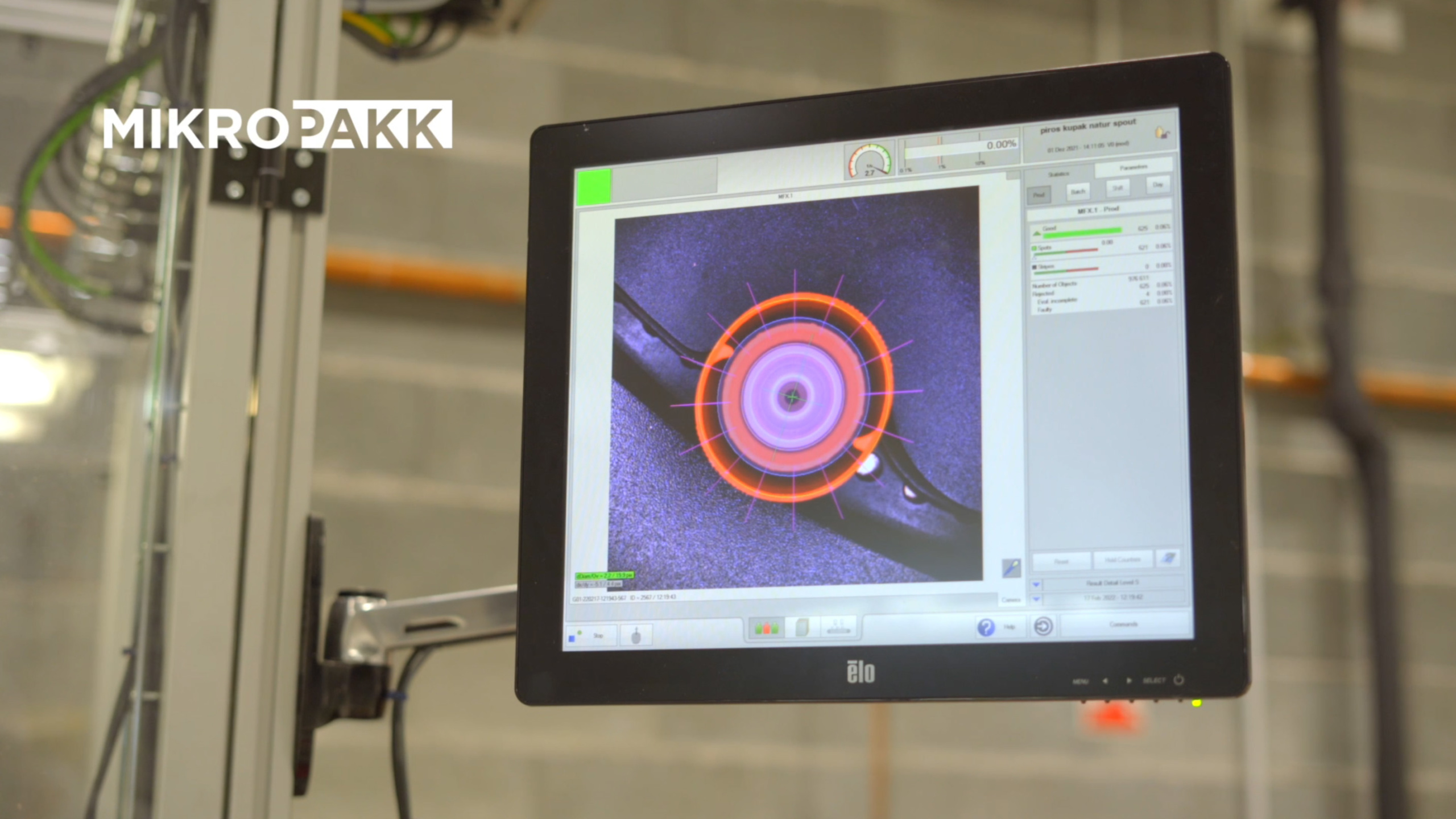
What quality assurance systems do we use?
We supply products to multiple industries, requiring diverse measurement approaches. Thus, we employ comprehensive and detailed quality control systems and procedures at every stage of the manufacturing process.
As part of the auditing process, we use 3D measuring equipment, that is crucial from the design phase of injection molding tools and is indispensable in the development and introduction of new products. Our clients can also request regular 3D reviews.
In addition to our quality control processes, we use:
- optical measuring device,
- laser 3D scanner,
- force and spring force gauges,
- colourimeters,
- surface roughness meter,
- modular flow index (MFI) meter,
- torque measuring devices.
For parameters that require tools we do not possess, we conduct tests through accredited laboratories and in partnership with the Budapest University of Technology and Economics.
Besides working exclusively with non-hazardous materials certified by external partners, we also perform migration tests during the manufacture of FMCG products.
Environmental awareness and sustainability in manufacturing
We are committed to ecological sustainability and resource efficiency.
Our approach emphasises the maximal reuse of materials: defective products from the manufacturing process are instantly ground up and, with client approval, recycled back into the production mix to facilitate in-line recycling.
This method ensures minimal production waste and hazardous waste. We actively incorporate post-industrial recycled (PIR) and post-consumer recycled (PCR) materials, consistently increasing the share of products made with these sustainable resources.
Additionally, each of our machines and electrically powered workstations is equipped with individual meters to enhance energy efficiency. We repurpose the waste heat from injection molding to heat our facilities, eliminating our reliance on natural gas for nearly 15 years.
By installing solar panels at our sites, we have significantly reduced our electrical energy use. Our manufacturing processes employ electromechanical drive machines, offering 20-40% energy savings over traditional hydraulic injection molding machines.