Globally, automation is increasingly shaping the development of the plastics industry, where rising quality expectations and intense competition drive companies to constantly seek new technological opportunities. Innovation and packaging automation are of strategic importance, as these are the keys to gaining and maintaining a competitive edge.
Due to specific conditions in most developed countries —such as higher energy prices and shortages in labor—extra emphasis must be placed on automation to ensure these challenges do not hinder our competitiveness. In this blog post, discover what production automation solutions we implement from the very first steps of product development and manufacturing to effectively support our partners.
Unique Production Automation Ideas from the First Step of Product Development
At our company, product development and automation go hand in hand from the very beginning. During the quotation process, we calculate both tooling and automation costs, as the two are closely linked. Component design, fitting points, and manufacturing solutions are all developed within a unified system.
As soon as the kick-off meeting ends, our automation engineering team is present, so initial ideas and potential technical solutions are brought to the table early. This is especially important for products consisting of multiple components that require assembly, where early automation planning is essential.
Our team develops customized solutions tailored to the product’s specifications. Whether through in-house development or by involving an external integrator, we always offer targeted solutions adapted to the product’s unique features, taking into account industry standards and requirements.
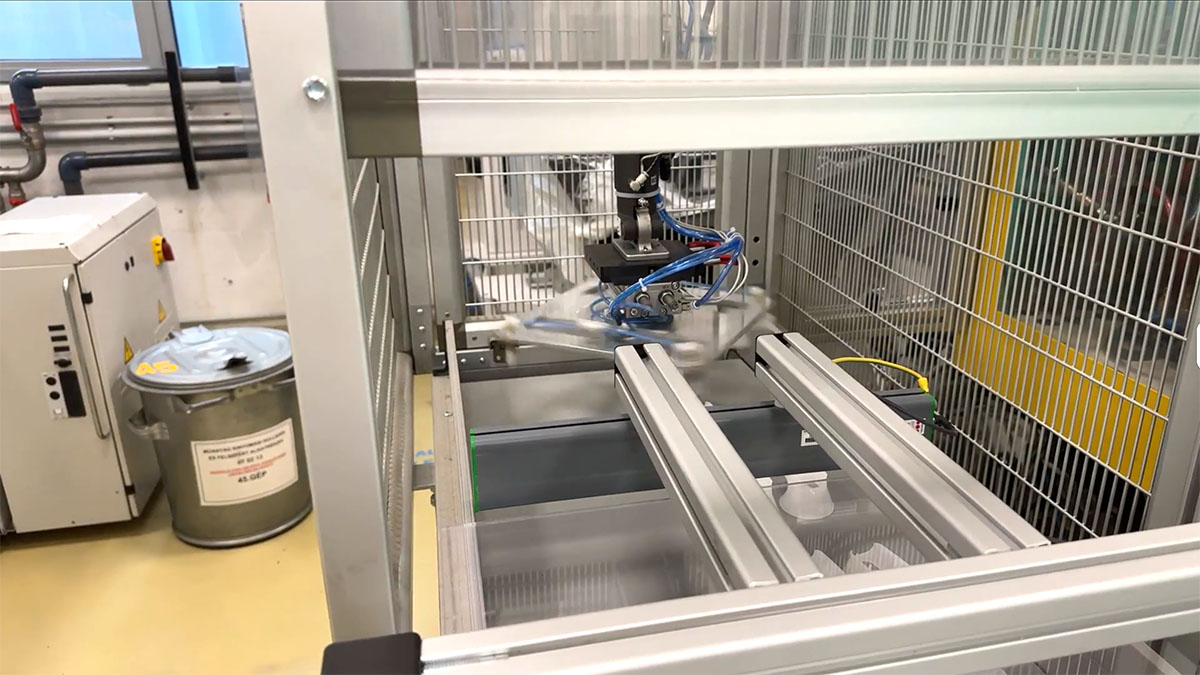
Linear robotic arm for automating packaging and assembly tasks
Automated Solutions for Flexible Production
Our goal is to achieve stable quality, fast production, and reduced unit costs. We support this with various automation solutions, which fall into two main categories:
- In-line (occurring directly at the injection molding machine)
- Off-line (taking place on a separate assembly line)
All our injection molding machines are supported by 3-axis linear robots, which are suitable not only for handling finished parts but also for boxing, quality control, or even dosing and implementing inserts. These are simple, universal solutions that significantly reduce the impact of labor shortages.
A good example of in-line automation is the assembly of the GENIUS PU foam integrated grip adaptor, where the entire assembly process—from feeding and bending the tube, to inserting the glove, to leaking and final testing—is fully automated with continuous quality control.
With our modular systems, we can quickly respond to changes in production demands: if necessary, we upgrade a semi-automatic system to a fully automated one, or set up new production cells.
The assembly and surface printing of the five-plastic-part TDS product presented a significant challenge—dense text had to be printed on a curved surface.
Initially, an operator checked the readability, but later we implemented an AI-based visual inspection system, which significantly reduced the reject rate. Demand for the product increased significantly compared to previous expectations, so the semi-automatic system was replaced by a fully automated one – and then, due to further increase in annual demand, the semi-automatic system was put back into operation.
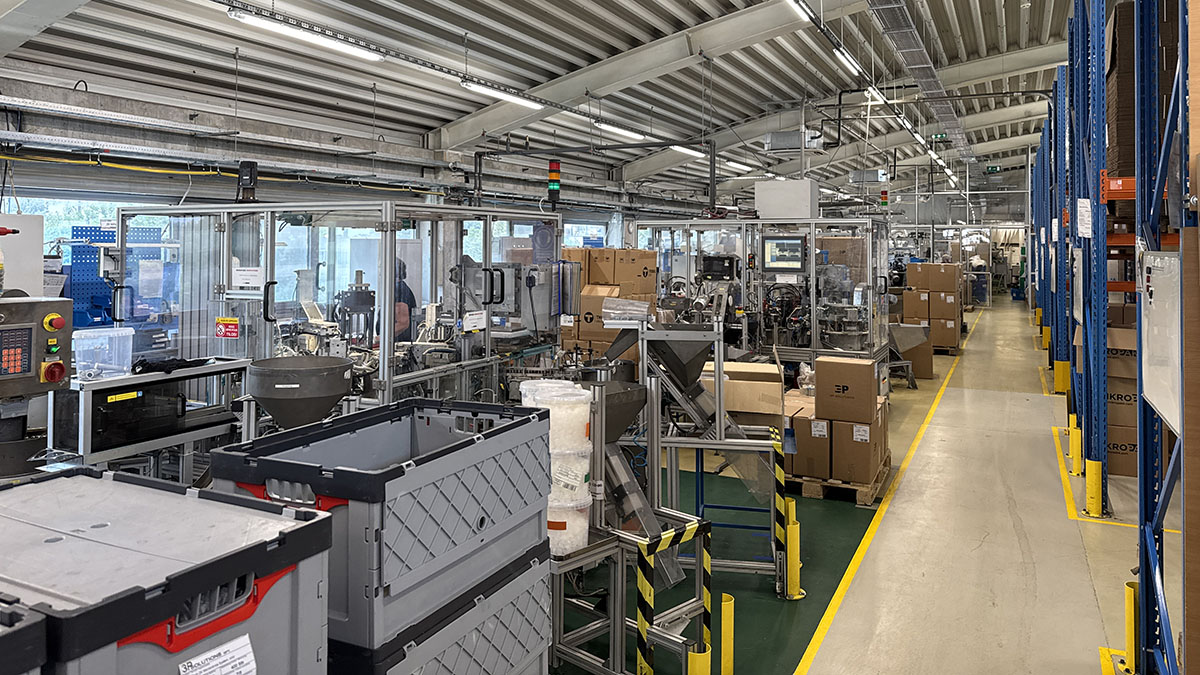
Automated assembly cells for flexible production and 100% quality control
Quality Control with 100% Accuracy
Automated quality control based on machine vision is also part of our system—smart cameras and AI algorithms filter out defective items during the cycle, ensuring 100% inspection. This is especially important for checking:
- Dimensional accuracy
- Proper filling
- Electronic contacts
It also drastically reduces the number of rejects resulting from manual inspection.
All this is not just a matter of technological advancement: global competition, increasing volume demands, and labor shortages are all factors that can no longer be managed effectively without automation.
We design and implement our automation projects in-house, including custom machines, assembly cells, and units performing specialized tasks.
We also consider sustainability aspects, such as waste management solutions suitable for recycling.
Sustainable, In-House Production Automation
If you are looking for solutions for product packaging automation, production optimization, or expanding production to meet growing demand, feel free to contact us! Our experienced team will support you from idea to implementation with customized, efficient solutions.