One of the most popular materials used in the construction industry is polyurethane (PU) foam in aerosol bottle packaging due to its excellent thermal and sound insulation properties. However, dispensing can be problematic as the material can bind and dry in the bottle, hindering efficient and cost-effective use.
We have developed several solutions to address this issue in collaboration with product manufacturers. As a result, we created the innovative Trigger hand adaptor, manufactured at our Salgótarján plant. The development enables more efficient dispensing and application of PU foam, resulting in significant advantages for everyday usage.
How does the Trigger plastic dispensing adaptor work?
The PU foam plastic dispensing adaptor is a handy tool that our partner sells packaged with their product. After removing the protective cap from the bottle, the adaptor can be easily placed onto the valve by simply snapping it on. We designed and patented a membrane geometry for the adaptor, which enables it to act as a lever, to activate the valve built into the bottle, directing the material through the applicator tube.
The direction of the foam spread can be easily controlled with the applicator tube, that can be shortened according to the user’s needs. Unlike other products, the Trigger adaptor also features a safety stop that needs to be removed before use, thus minimising the likelihood of accidental activation. The plastic dispensing adaptor is marketed by Henkel with PU foam products intended for small-scale and private use. We provide our partner with fully automated
- manufacturing,
- assembly, and
- quality control
to ensure that the product reaches the end-user in the highest possible quality.
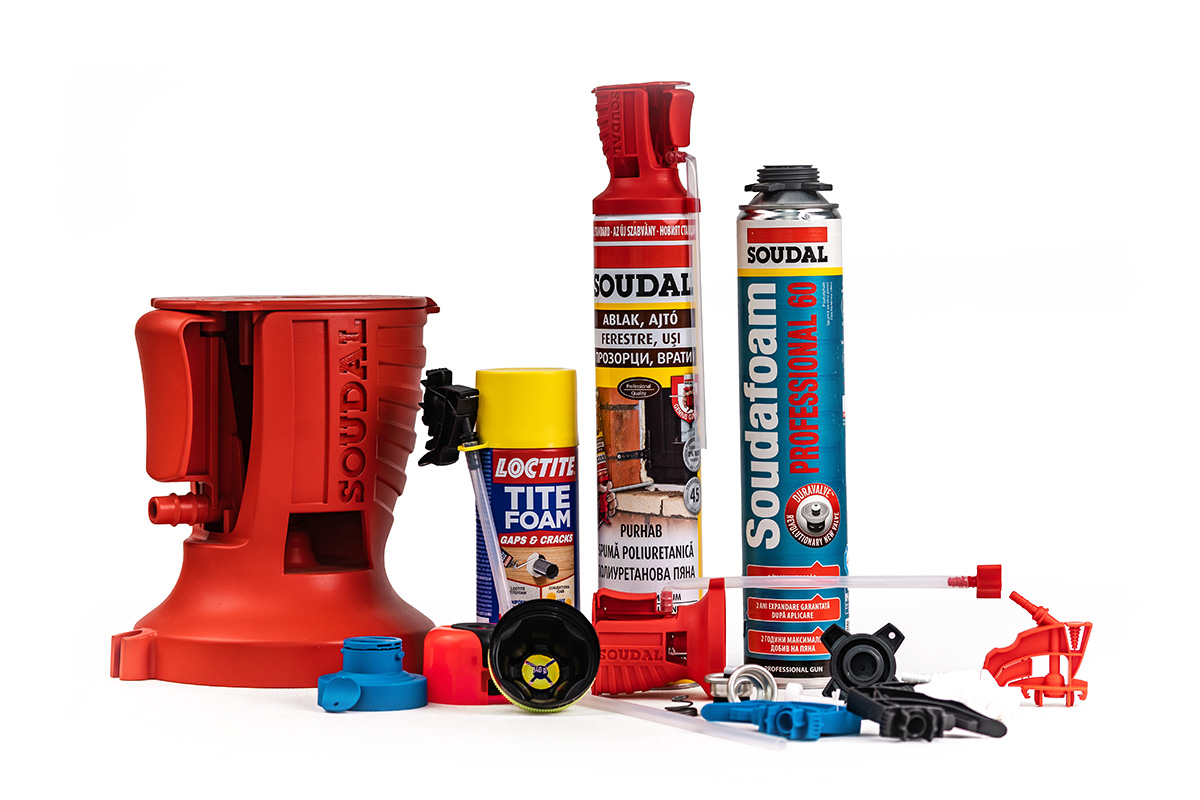
We have developed several solutions for efficient dispensing of two-component products
How we automated the production of Trigger plastic components?
The fully automated production of the plastic dispensing adaptor consists of two main steps. The first one is injection molding, where the adaptor is shaped in one go, including the bore. The second step is assembly, including quality control as an integral part of the process. Each step is fully automated, allowing high productivity, efficiency, and reliable manufacturing.
A linear robot lifts eight adaptors at once from the injection molding tool and places them on an intermediate table. The palletising SCARA robot then places them in pairs into the assembly machine and also lifts out the assembled and inspected products. The applicator tube, which is extruded in various sizes by our manufacturing partner, also arrives at this stage. The assembly machine fits the applicator tube onto the adaptor and tests the quality of the product.
The main challenge is automated quality control
During the fully automated production of the plastic dispensing adaptor, the greatest challenge is automated quality control. Before delivery, the following aspects must be checked:
- integrity of the bore,
- flexibility of the membrane, and
- sealing.
The testing is done with air; we block the applicator tube end and blow air into the product. Any pressure loss is measured, and if the product is not sealed, it is sorted out as defective. Then, we blow air through the open applicator to check the bore’s permeability by measuring the resistance.
The main challenge was to design and develop a testing mechanism that measures the quality of the product reliably, accurately, and with short cycle times.
The high-quality products are packed and delivered to the customer.
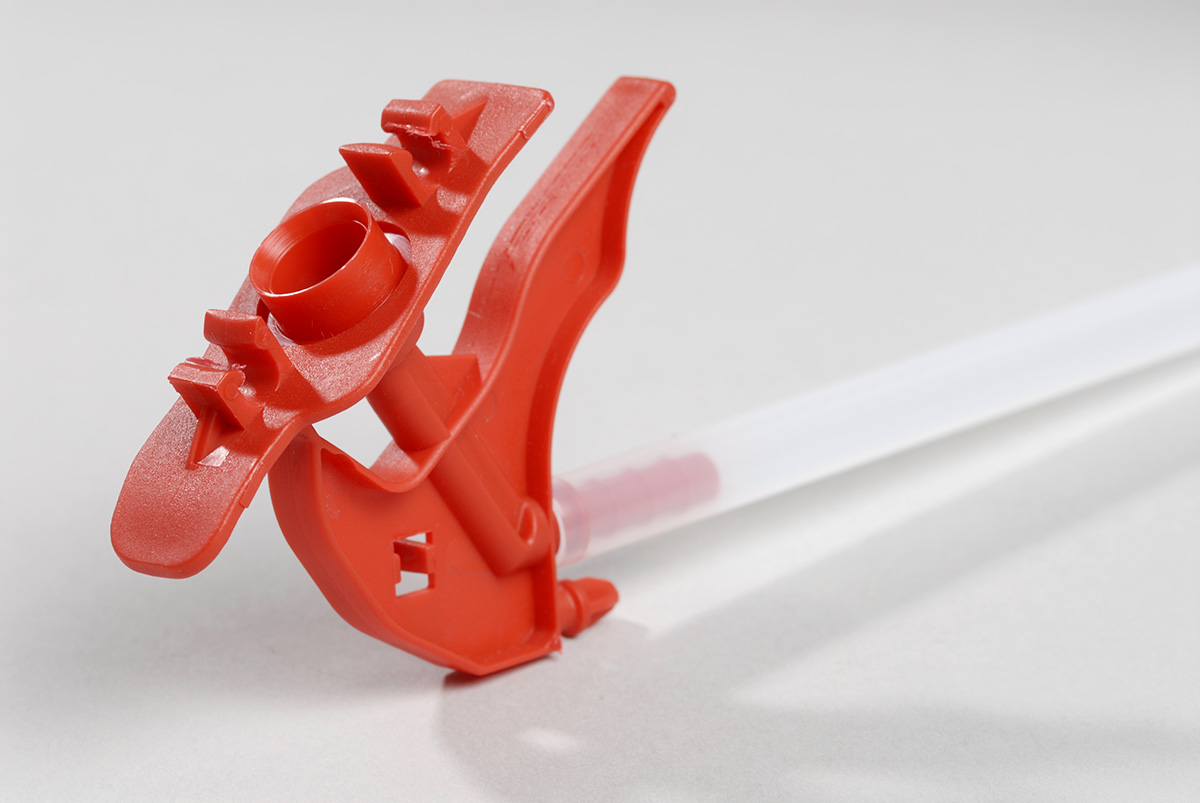
Ready-made dispensing adaptor with applicator tube – manufactured in several colours
Automated production and quality control results in a successful product
The plastic dispensing adaptor has been manufactured in Salgótarján since 2021, the production line can manufacture millions of this product monthly. Colour may vary per series, according to customer demands. The continuous development of new-generation dispenser adaptor solutions ensures growth in production as well as technological advancement.
Mikropakk innovation at the service of partners
Mikropakk offers a wide range of dispensing adaptors, manufactured in various versions. We customise our products according to our customers’ needs, including the bottle and dispenser head type. The adaptor is compatible with our valve system, but we can also adapt to other systems. Whether it’s introducing a new product, improving existing solutions, or engineering and developing new ones, we’re prepared to face any challenge.
Our production process is versatile and can handle both small-scale product development and large-scale manufacturing to meet all of our customers’ requirements.